Precision Die Casting Solutions Built for Performance and Scale
At Harbor Labs, we specialize in the design, production, and supply of precision die cast metal parts that meet the toughest performance standards. From concept to tooling, production to finishing, our die casting solutions are engineered to reduce lead times, eliminate quality variance, and optimize cost per unit — without compromise. Whether you require lightweight structural components or aesthetically-finished housings, we work across a global supply chain to deliver ISO:9001 certified die cast parts in aluminum, magnesium, zinc, and other non-ferrous alloys — tailored for sectors like automotive, lighting, construction, and industrial equipment.
What Is Die Casting?
Die casting is an efficient and highly accurate process used to create complex metal parts through high-pressure injection of molten metal into reusable steel molds — or “dies.” It enables tight tolerances, high production rates, and excellent repeatability, making it ideal for applications that demand both structural strength and fine detail.
Depending on the metal and part geometry, Harbor Labs offers both:
- Hot-Chamber Die Casting: For low-melting-point alloys like zinc
- Cold-Chamber Die Casting: For high-melting-point alloys like aluminum and brass
Post-injection, parts are cooled rapidly to form high-integrity components that are either ready for assembly or require minimal finishing.
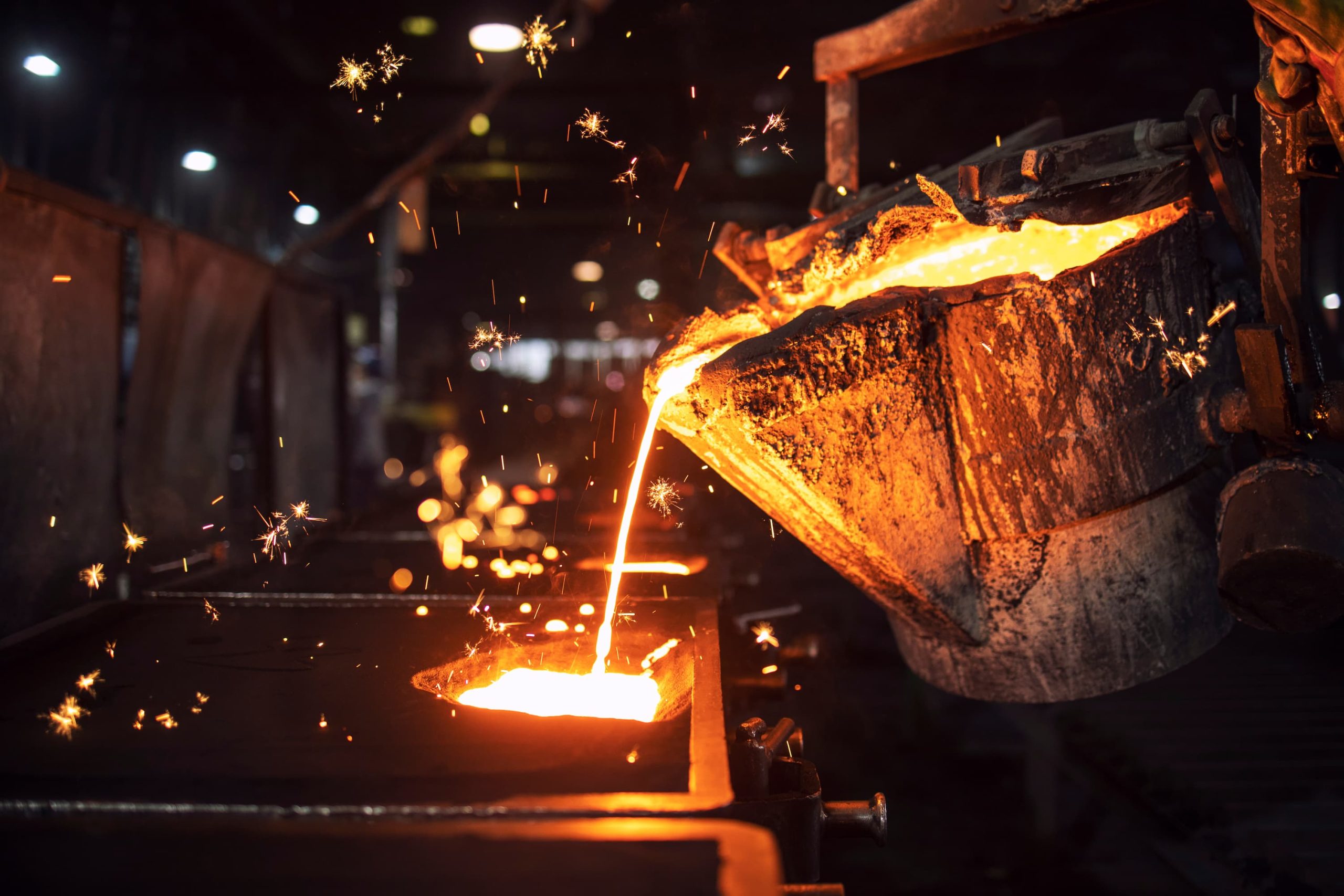
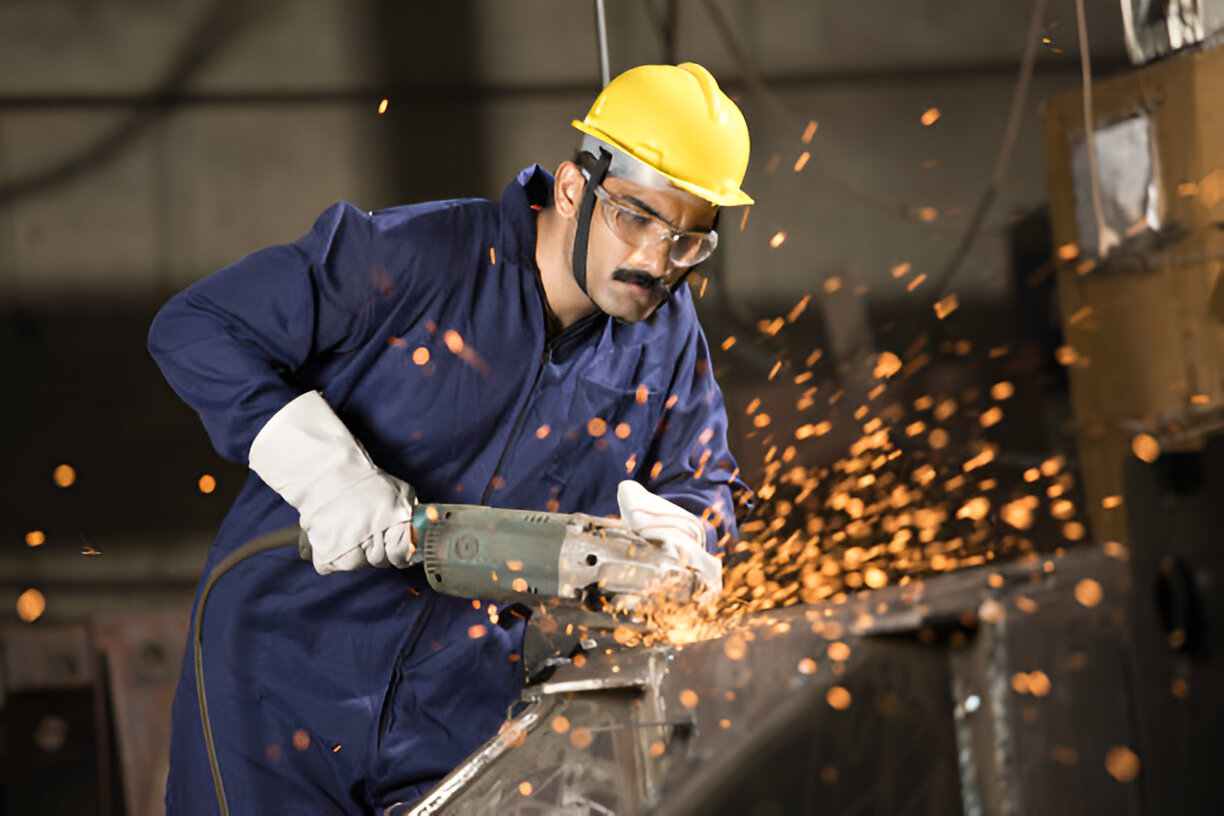
Why Harbor Labs for Die Casting?
✔ ISO:9001 Certified Global Network
We operate with internationally recognized quality systems to ensure compliance, reliability, and traceability.
✔ End-to-End Project Support
From die design to production oversight, our engineers are involved at every stage to ensure precision and performance.
✔ Multi-Alloy Expertise
We manufacture in a wide range of non-ferrous metals including:
- Aluminum
- Magnesium
- Zinc
- Brass
- Copper
✔ Industry-Focused Applications
We produce high-performance die cast parts tailored for:
- Automotive (transmissions, housings, engine components)
- Lighting (heat sinks, enclosures)
- Construction (fittings, structural brackets)
- General industrial equipment
✔ Speed & Efficiency at Scale
Our global sourcing strategy enables faster production cycles, minimized tooling delays, and consistent quality — delivered worldwide.
Benefits of Die Casting with Harbor Labs
- Complex shapes produced with high repeatability and tighter tolerances than many other mass-production methods
- Reduced post-processing and minimal need for machining
- Stronger, lighter parts compared to plastic injection molding or traditional casting techniques
- Capability to cast thin walls and integrated features such as threads, bosses, or inserts
- High aesthetic quality and smoother surface finishes
- High-volume production with long-lasting dies and consistent quality over thousands of cycles
Cost-effective manufacturing with reduced waste and faster time-to-market
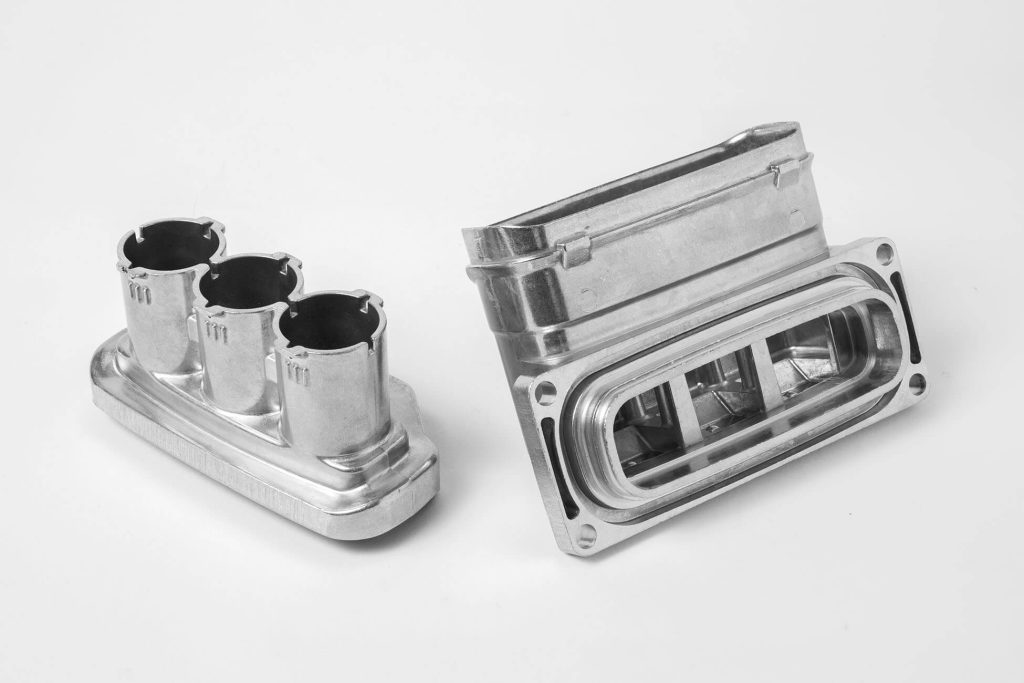
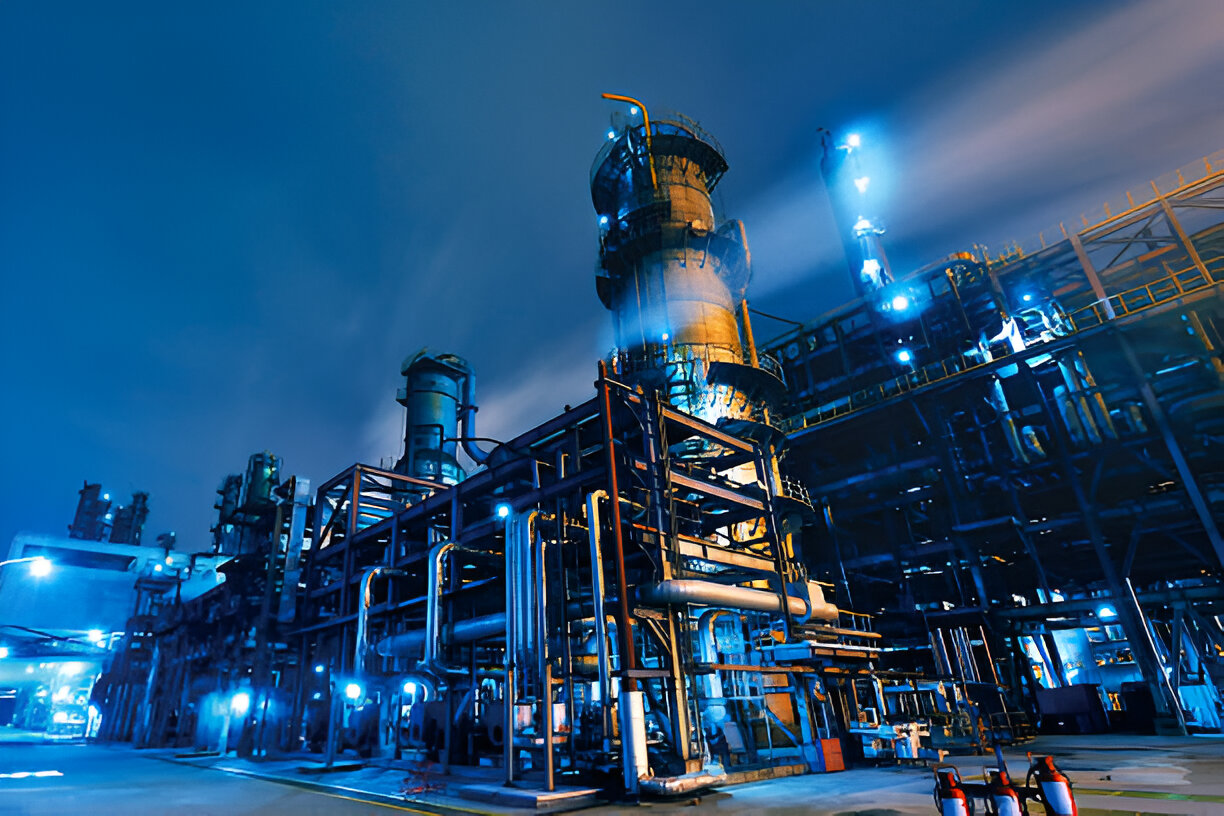
Technical Capabilities
Production Methods Supported:
- High-pressure die casting
- Gravity die casting
- Insert casting
- Multi-cavity tooling
- Secondary operations (trimming, deburring, shot blasting)
Common Applications:
- Engine blocks, gearbox housings, and brackets (automotive)
- LED housing and fixtures (lighting)
Wall mounts, window hardware, and framing supports (construction)