Mass-Produced Precision: Investment Castings that Outperform Expectations
When design complexity meets volume demand, investment casting becomes the optimal manufacturing method. At Harbor Labs, we offer highly precise, ISO-certified investment casting solutions across a range of metals and alloys. Backed by engineering support and global sourcing expertise, we help OEMs and manufacturers mass-produce small and mid-size parts with consistency and confidence. Our clients rely on us for tight-tolerance, near-net-shape parts with exceptional surface finishes — from delicate turbine vanes to high-pressure tubing and intricate medical or defense components.
What Is Investment Casting?
Investment casting, also known as lost-wax casting, is a manufacturing process used to produce complex metal parts with superior surface finishes and tight tolerances. The process involves creating a wax model, building a ceramic mold around it, and then pouring molten metal into the mold once the wax is melted away.
- Suitable for intricate parts, delicate features, and undercuts
- Supports wall thicknesses as low as 0.025 in.
- Offers dimensional tolerances of ±0.003 in/in
- Eliminates the need for welding or assembling multiple parts
- Enables thin-walled, lightweight, yet strong component design
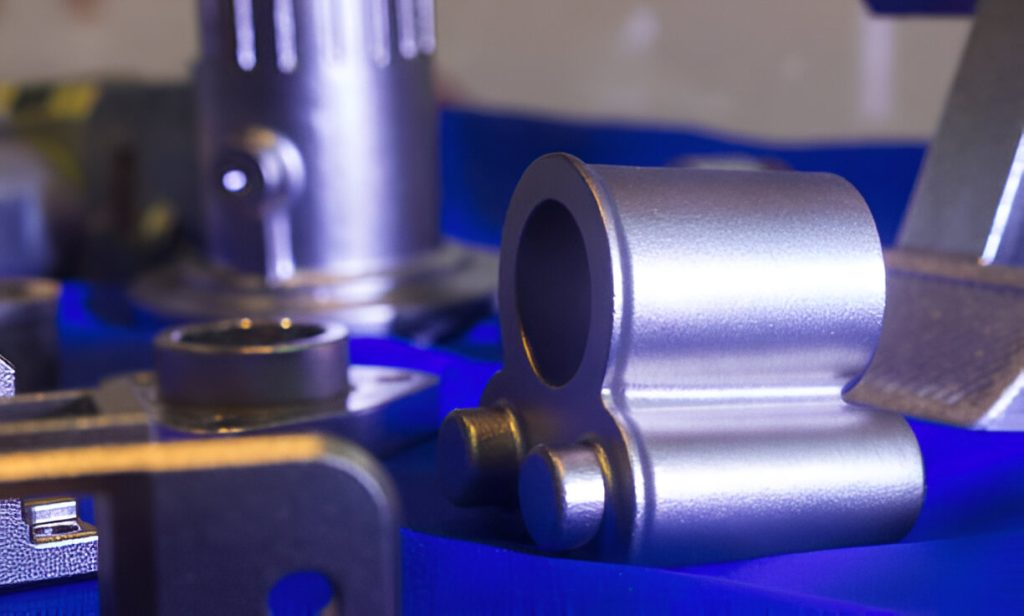
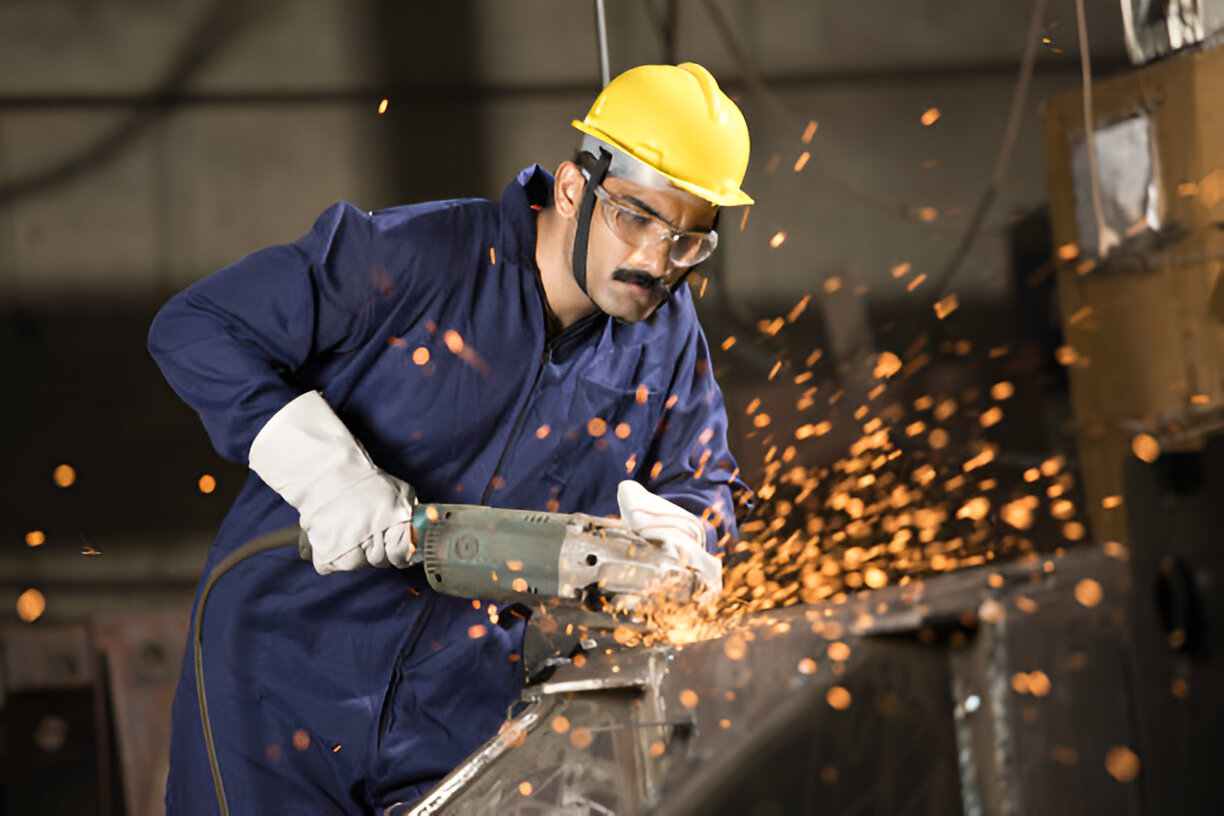
Why Choose Harbor Labs for Investment Casting?
- Precision at Scale
From small batches to large production runs, we help scale investment cast components with unmatched consistency and minimal defects. - Complex Geometries Made Simple
We specialize in intricate shapes, undercuts, and tight radii that other casting methods struggle to achieve — without expensive tooling modifications. - Surface Finish Excellence
Investment castings feature superior surface smoothness compared to sand or permanent mold casting, often eliminating the need for machining. - Dimensional Accuracy with Minimal Machining
Parts come out of the mold extremely close to final dimensions, minimizing secondary operations and speeding up the supply chain. - Global Supplier Network
Our casting partners are rigorously vetted and ISO 9001–certified, ensuring repeatable quality across thousands of units. - Faster Speed-to-Market
With rapid prototyping and scalable production plans, we cut down your product lead time — without compromising quality or cost.
Benefits of Investment Casting
- Produces highly detailed and dimensionally stable parts
- Allows for consolidation of multiple parts into one monolithic design
- Reduces machining and finishing requirements
- Enables production of parts with thin walls and complex forms
- Eliminates need for joints, welds, or fasteners
- Ensures smooth surfaces without visible parting lines
- Offers excellent material utilization with low waste
- Suitable for high-precision applications across industries
- Delivers a wide range of sizes — from tiny medical parts to larger aerospace components
- High repeatability across large production volumes
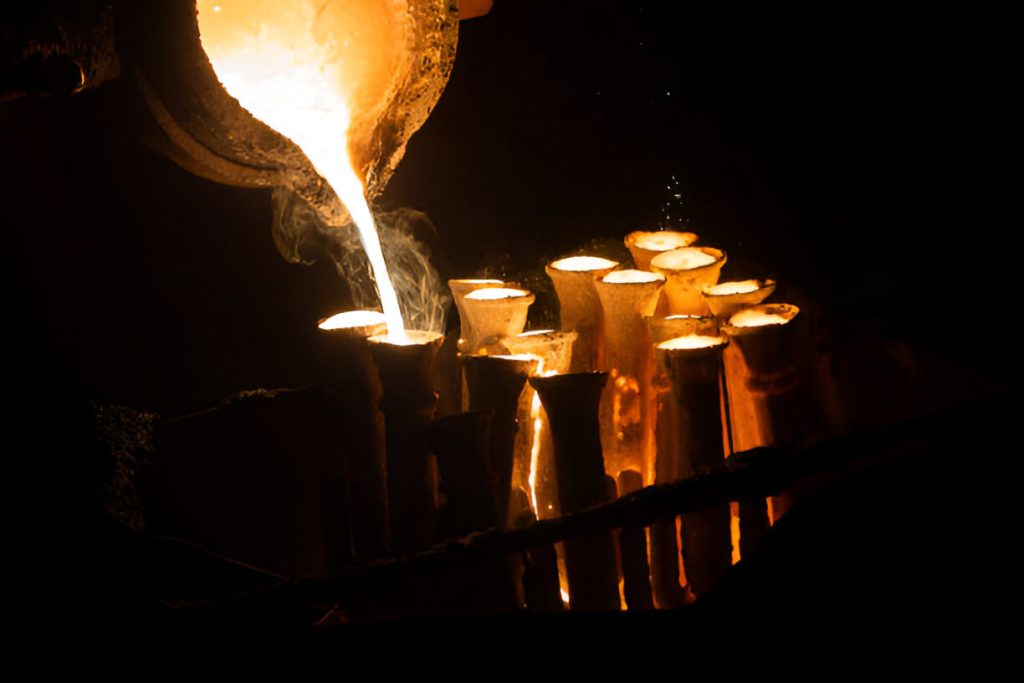
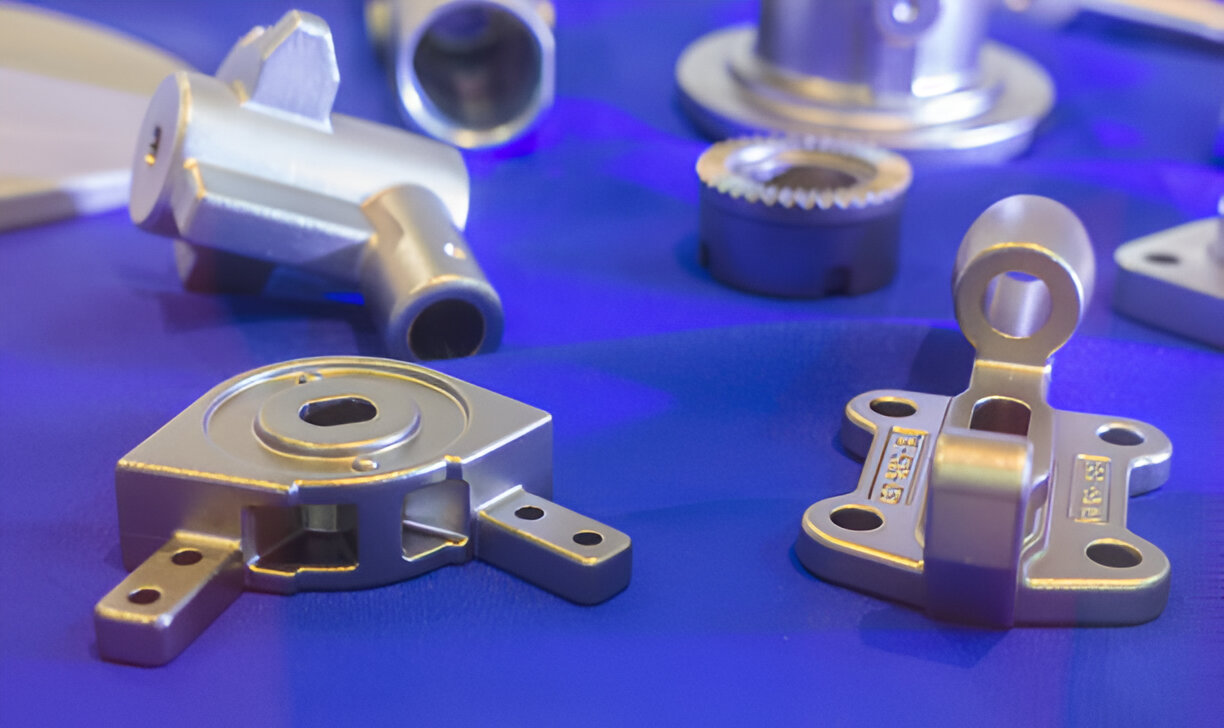
Common Applications
- Aerospace: blades, housings, nozzle guides
- Automotive: turbocharger wheels, rocker arms, gearbox components
- Medical Devices: orthopedic implants, surgical tools
- Industrial Equipment: valves, pump impellers, heat-resistant parts
- Defense: sighting systems, weapon housings, brackets
- Oil & Gas: precision tubing, couplings, and pressure-retaining parts
Materials We Work With
- Carbon Steel
- Stainless Steel
- Nickel Alloys
- Ductile Iron
- Grey Iron]
- Cobalt-Chromium
- Superalloys (on request)
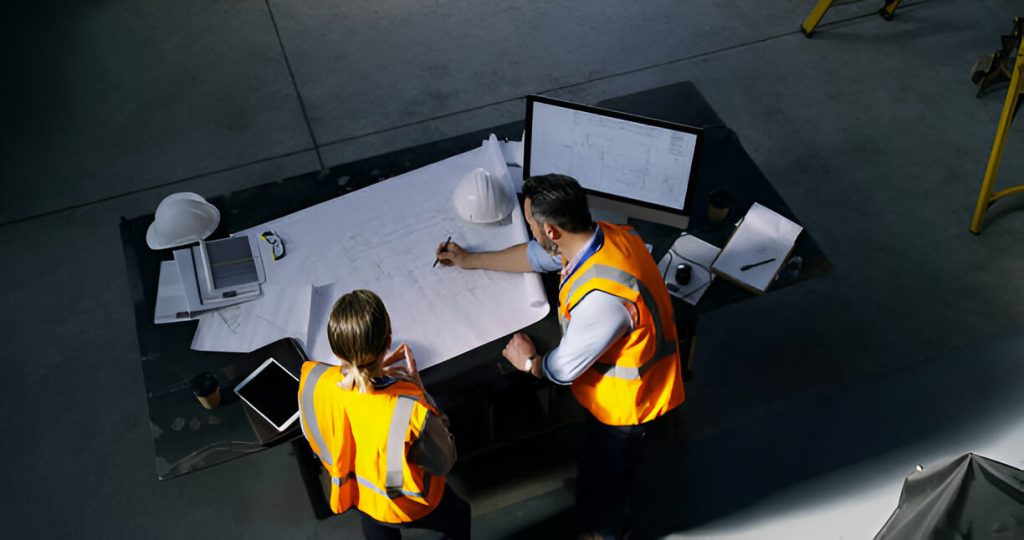