Design Smarter. Engineer Better. Build Faster.
Behind every high-performing product is great engineering — and that’s where Harbor Labs begins. As the driving force of everything we manufacture, our Product Design & Engineering Innovation team ensures your products are not just manufacturable, but optimized for performance, cost-efficiency, and scalability. Whether you're starting from a napkin sketch or iterating on a legacy design, our engineers work as an extension of your team — bridging the gap between R&D and global production. We blend mechanical design, tooling strategy, and materials expertise to help you innovate, iterate, and industrialize at speed. Whether you require lightweight structural components or aesthetically-finished housings, we work across a global supply chain to deliver ISO:9001 certified die cast parts in aluminum, magnesium, zinc, and other non-ferrous alloys — tailored for sectors like automotive, lighting, construction, and industrial equipment.
Our Core Capabilities
- DFM & DFA Consulting : We refine designs for manufacturability and assembly — reducing costs, improving quality, and shortening lead times across processes.
- CAD / CAE / 3D Modelling : Our engineers build detailed part and tooling models using SolidWorks, AutoCAD, Creo, and Fusion 360 — with real-time collaboration and rapid iteration.
- Prototyping & Rapid Validation : From 3D printing to CNC machined prototypes, we accelerate product testing cycles to validate form, fit, and function before full-scale production.
- Material Selection & Testing : We help you choose the right materials based on strength, cost, corrosion resistance, and process compatibility — verified by third-party lab reports.
- Tooling Design & Simulation : Design and simulate high-precision tools, dies, and molds for casting, forging, and extrusion. We reduce rework and speed up production readiness.
- Reverse Engineering : Have a legacy component with no documentation? Our team can digitize, redesign, and improve existing parts to extend product life or reduce costs.
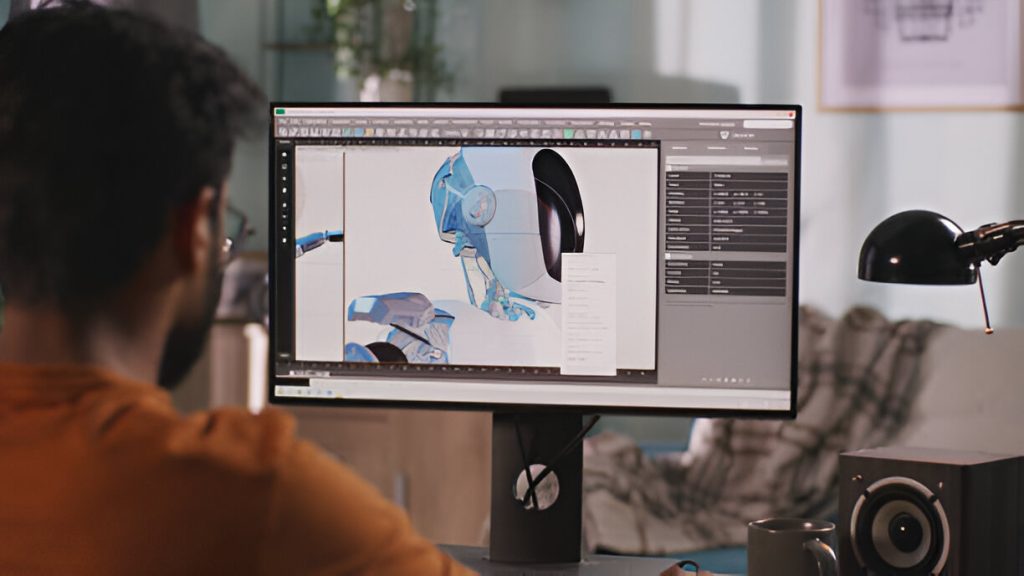
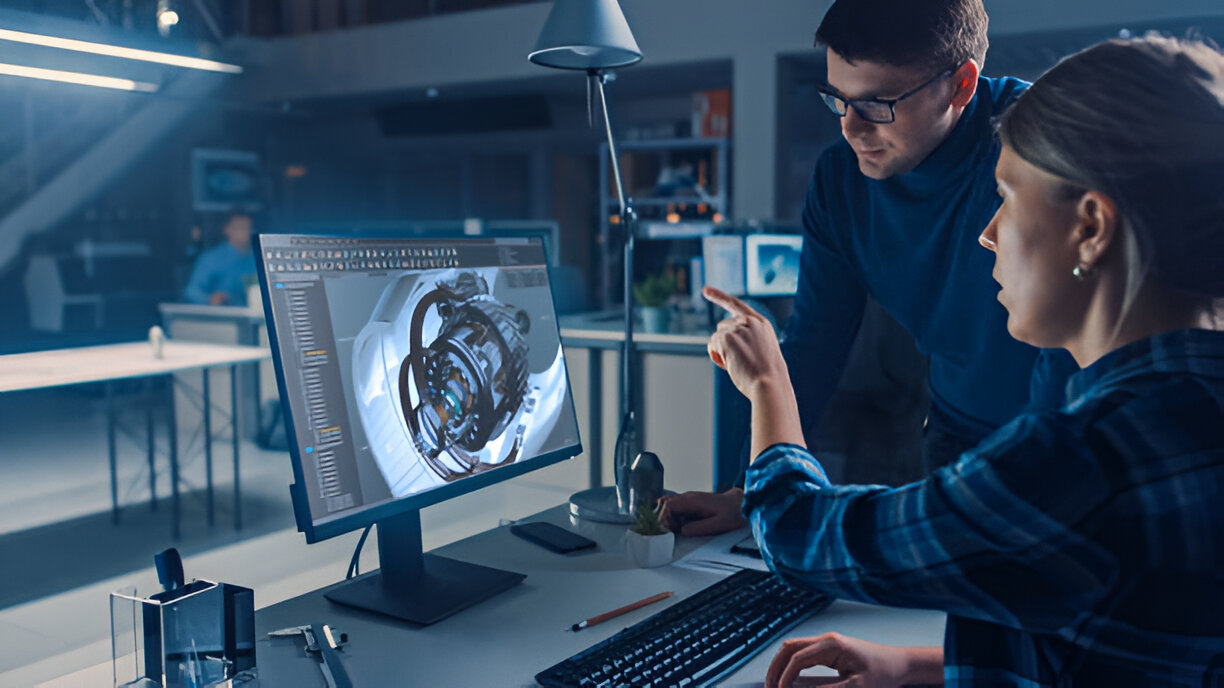
End-to-End Engineering Support
Harbor Labs doesn’t just hand over blueprints — we own the outcome. Our engineers work with your teams from design freeze to first article inspection, helping de-risk the transition from prototype to mass production.
- Integrated with global manufacturing timelines
- Seamless handoff to suppliers for tooling and sampling
- Real-time tracking, feedback, and engineering changes
- Design change validation and document control
Where Innovation Meets Execution
Our engineering capabilities power innovation across demanding, high-performance sectors:
- Automotive: Lightweight structures, EV-ready components, thermal and strength optimization
- Lighting: Modular assemblies, heat dissipation systems, tool-free fixture design
- Industrial Equipment: Structural integrity, vibration resistance, field-tested durability
- Construction: High-load components, ease of installation, regional code compliance
- Consumer Products: Ergonomics, aesthetics, design-for-cost and scalability
- Defence & Aerospace: Precision-engineered parts with tight tolerances, material certifications, and mission-critical reliability
- Automotive: Lightweight structures, EV-ready components, thermal and strength optimization
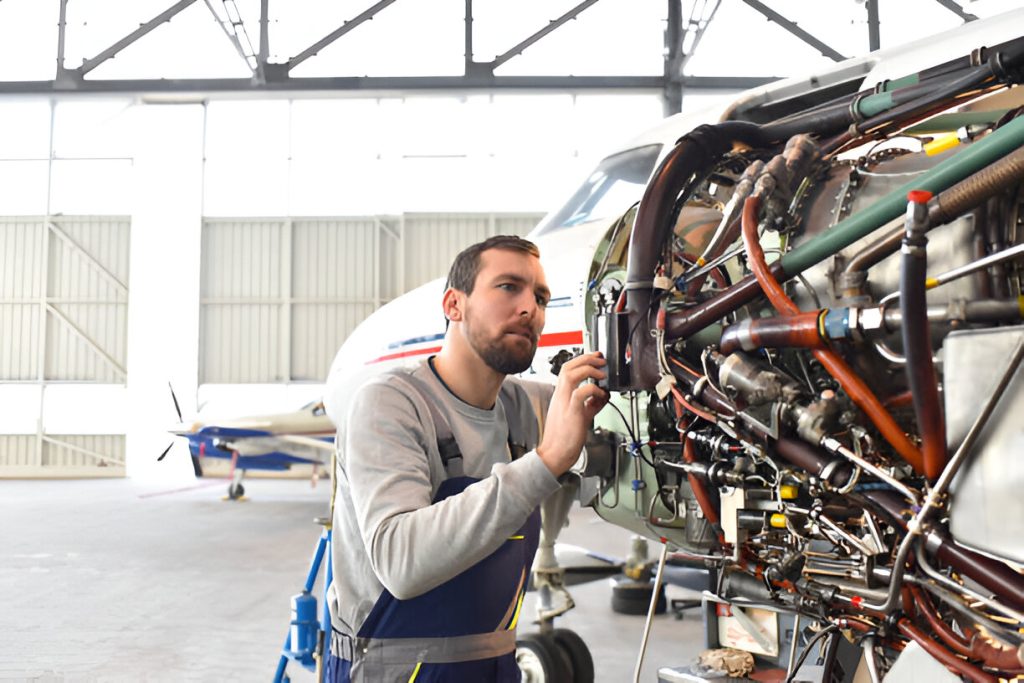
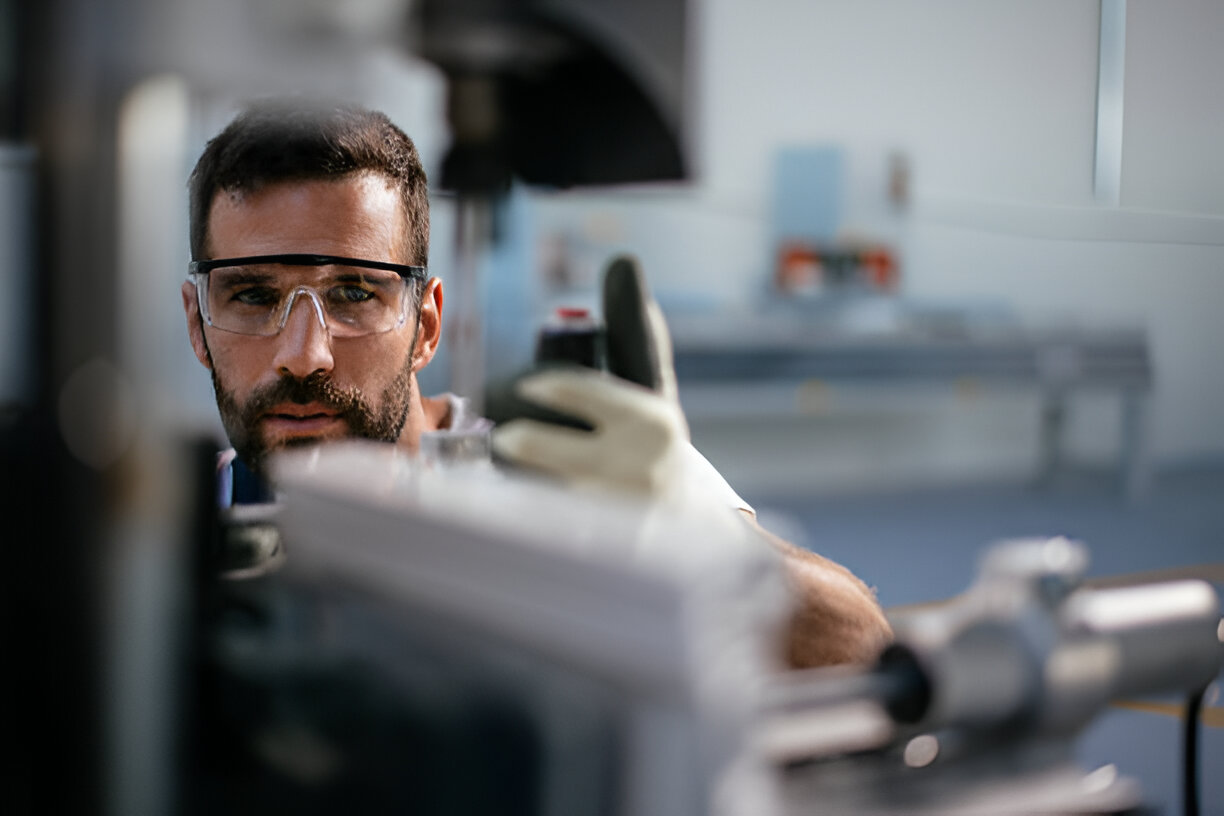
Why Choose Harbor Labs for Design & Engineering?
- Start-to-Scale Thinking – We don’t just design for today — we design for mass production at scale
- Cross-Process Expertise – Deep integration with die casting, machining, forging, and more
- Global Engineering Footprint – Teams in the U.S. and India for 24/7 collaboration
- Faster Time to Market – Rapid iterations, prototyping, and validation
- Quality by Design – Every product is engineered to meet its performance, compliance, and cost targets from day one