Quality You Can Count On. Certifications That Back It Up
At Harbor Labs, quality isn’t a box we check—it’s a culture of accountability embedded into our entire sourcing and production ecosystem. From material selection to final delivery, our quality management systems are designed to meet and exceed global industrial standards, ensuring you receive reliable, high-tolerance parts every single time. Whether you're scaling production or sourcing offshore for the first time, we make it easy for your engineering and procurement teams to trust the output—because we control the input.
ISO-Certified Partners You Can Trust
We only work with suppliers who meet strict qualification criteria, including:
- ISO 9001: Quality Management Systems
- ISO/TS 16949: Automotive Quality Systems (for relevant parts)
- ISO 14001: Environmental Management (where applicable)
Every partner in our network is thoroughly audited by our quality and sourcing engineers. We assess and track their:
- Manufacturing capabilities and equipment health
- In-house QA protocols and tolerance control
- Compliance with international standards and customer requirements
Delivery and defect performance over time
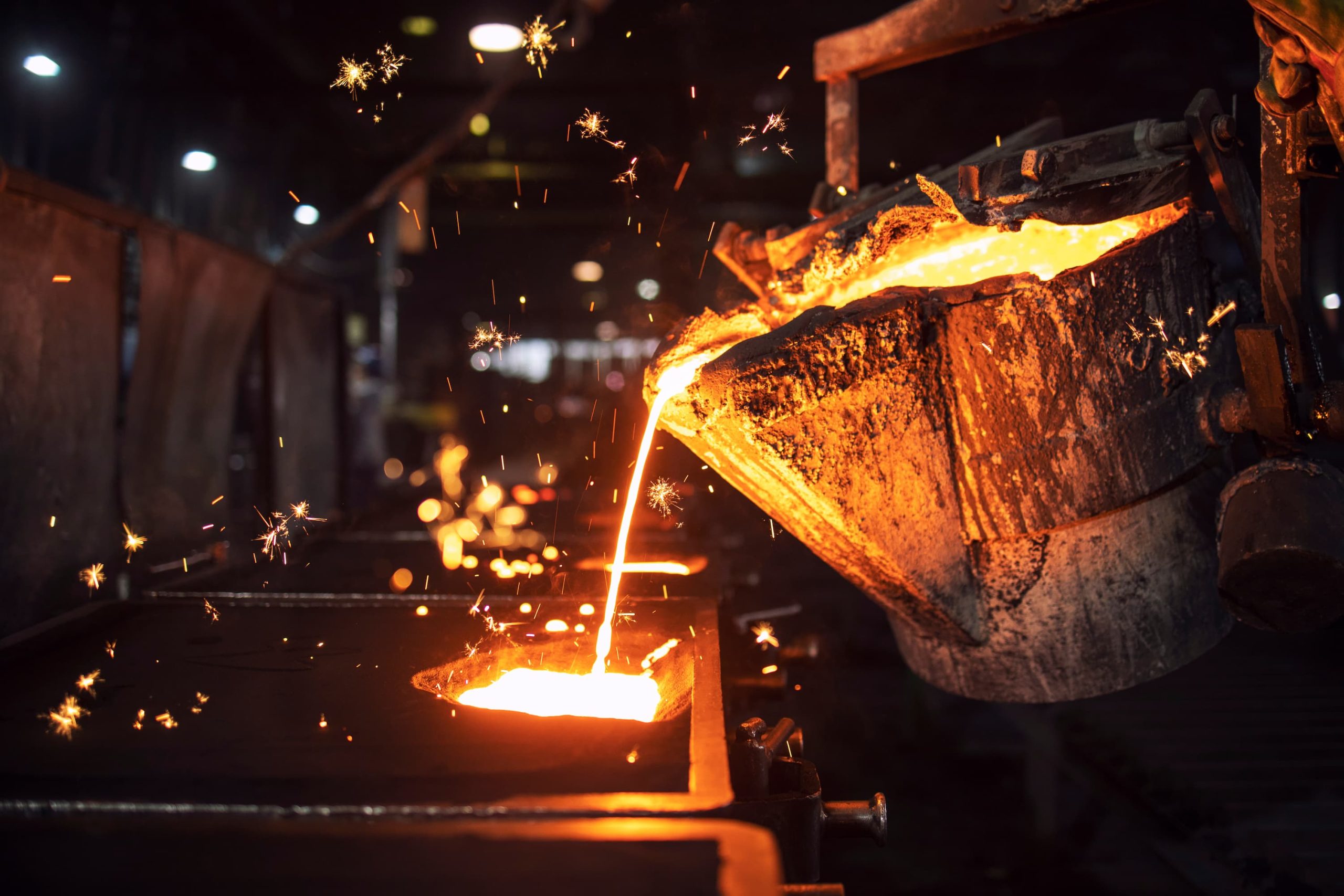
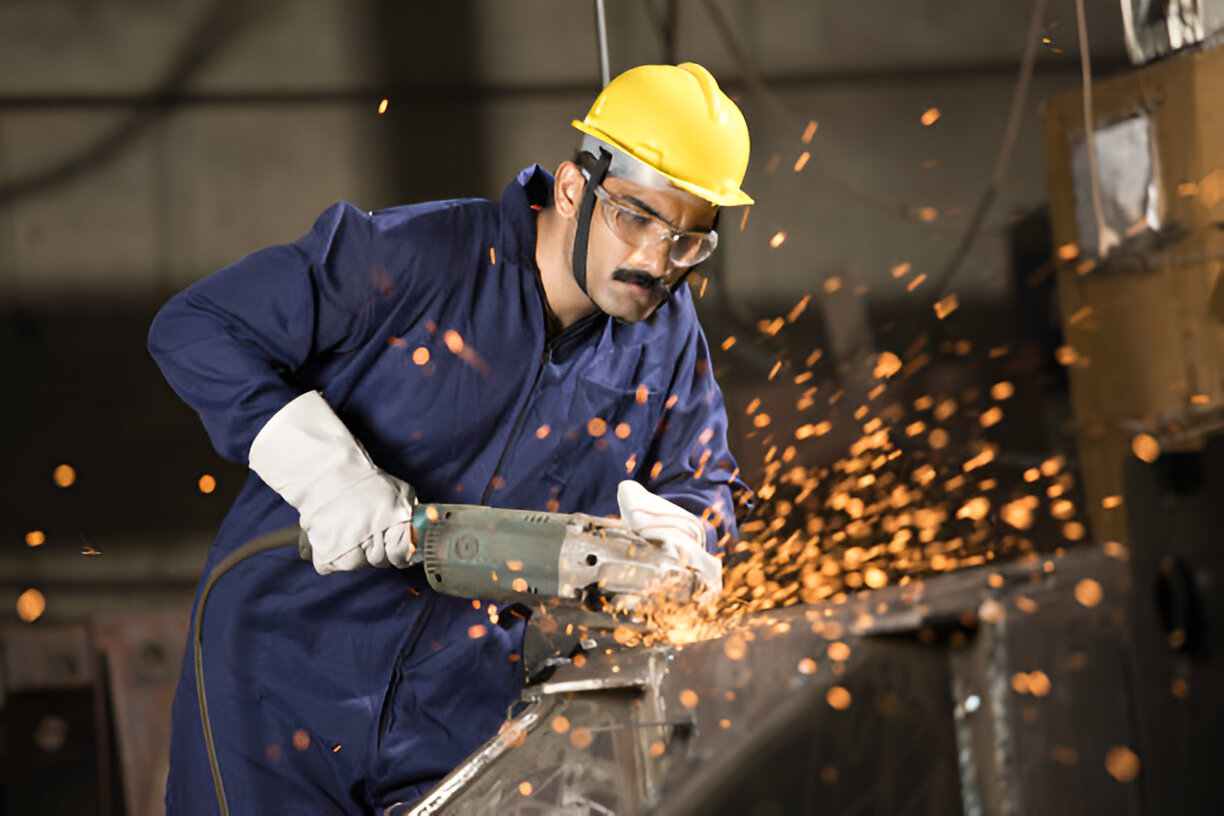
The Harbor Labs Quality Framework
We apply a layered QA model—designed to minimize defects, reduce rework, and eliminate waste—across every engagement:
- Engineering Validation
- Dedicated Harbor Labs engineers oversee supplier onboarding and part feasibility analysis
- Customer-approved tooling designs and specification alignment before kickoff
- Dedicated Harbor Labs engineers oversee supplier onboarding and part feasibility analysis
- Tooling & Process Controls
- In-person inspections during tooling manufacturing
- FMEA and process audits to ensure control of critical dimensions
- Real-time monitoring of production consistency and part traceability
- In-person inspections during tooling manufacturing
- Material & Dimensional Testing
- Third-party lab verification for raw materials
- Precision measurements using CMM, FAI, and SPC for dimensional integrity
- Visual and functional inspections before shipment
- Third-party lab verification for raw materials
- Benchmarking & Continuous Improvement
We compare our operational KPIs monthly against best-in-class suppliers worldwide to identify opportunities for:- Higher yield
- Lower PPM (parts per million defect rate)
- Reduced lead times and faster tooling readiness
- Higher yield
Lower total cost of ownership
Metrics We Track & Share
At Harbor Labs, transparency is non-negotiable. We openly benchmark and report on:
- On-Time Delivery Rate
- Defect Rate (PPM)
- Inventory Efficiency (Days of Supply)
- Warehousing and Handling Cost as % of Sales
We share these reports with customers, enabling continuous collaboration and mutual accountability.
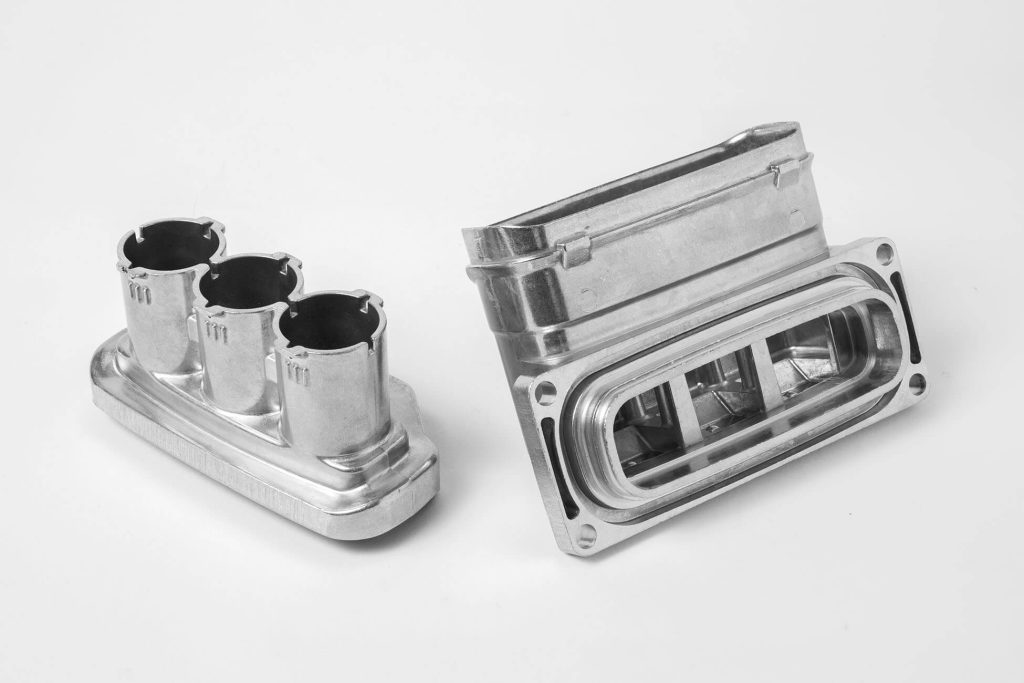
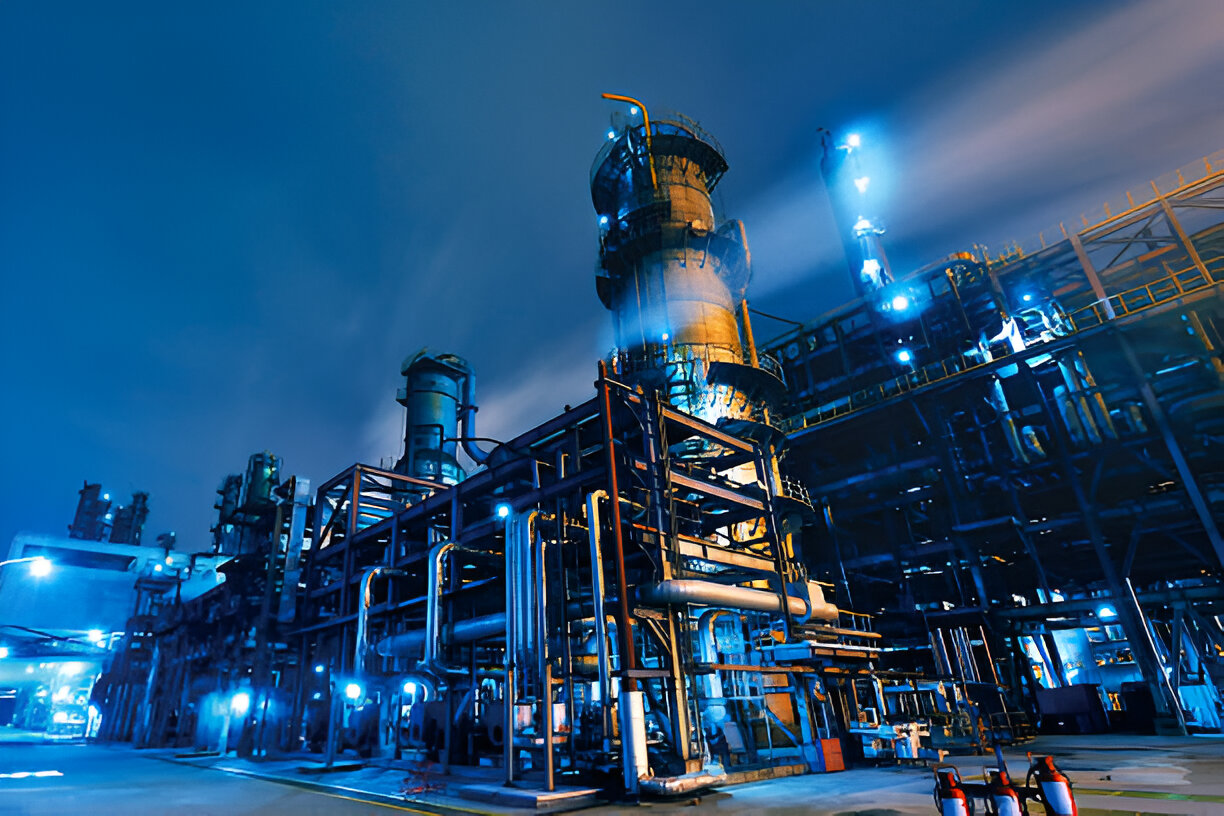
Customer-First QA Philosophy
Your standards are our starting line. We align our quality checkpoints with your specific industry requirements—whether it’s Tier 1 automotive, construction equipment, or industrial lighting. Our customer-centric QA programs include:
- 24/7 communication channels with our engineers
- Root cause analysis and CAPA (Corrective and Preventive Action) protocols
Final pre-shipment review and sign-off before dispatch