High-Strength Forged Parts Engineered for Performance and Durability
When the application demands maximum strength, exceptional fatigue resistance, and structural reliability — forging becomes the gold standard. At Harbor Labs, we deliver precision-engineered forged parts through a global network of ISO-certified forging facilities. From automotive axles to high-pressure valve bodies, we provide end-to-end solutions tailored to critical performance specifications. Our in-house engineering support and boots-on-the-ground supplier oversight ensure every component is optimized for grain structure, strength, and dimensional integrity — all while meeting global compliance and lead time benchmarks.
What Is Forging?
Forging is a metal forming process that uses compressive forces to shape materials into the desired geometry. This technique improves the internal grain structure of the part, resulting in enhanced tensile strength, fatigue resistance, and impact durability — far beyond what’s possible with casting or machining.
- Open-Die Forging – Suitable for large, simple geometries
- Closed-Die Forging – Ideal for precision parts with complex profiles
- Seamless Rolled Ring Forging – Specialized for rotational components like gears, rings, and bearings
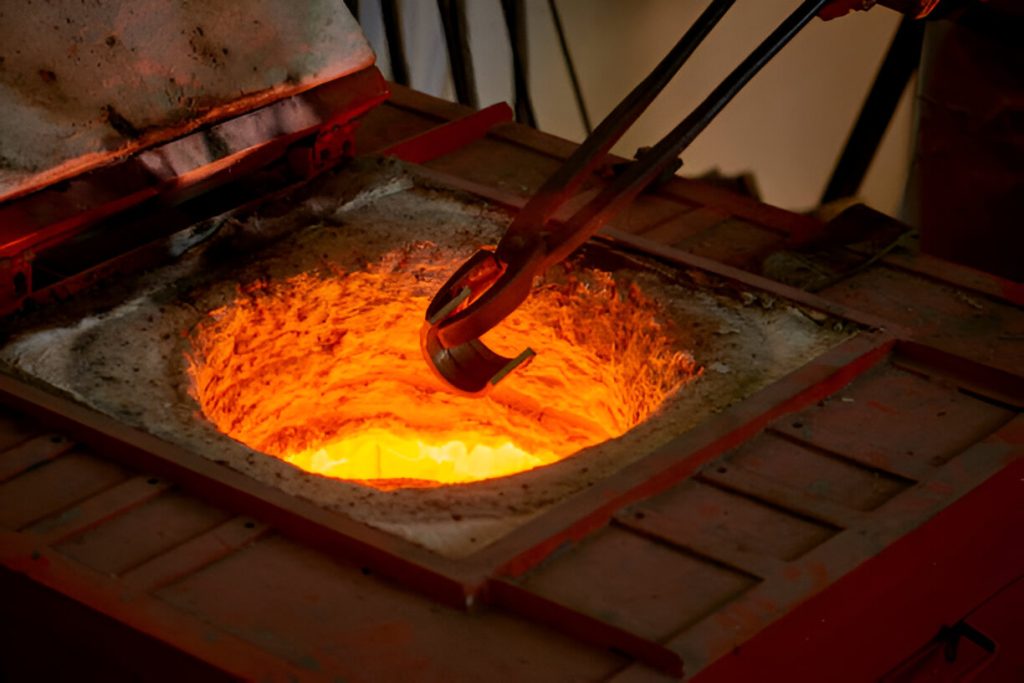
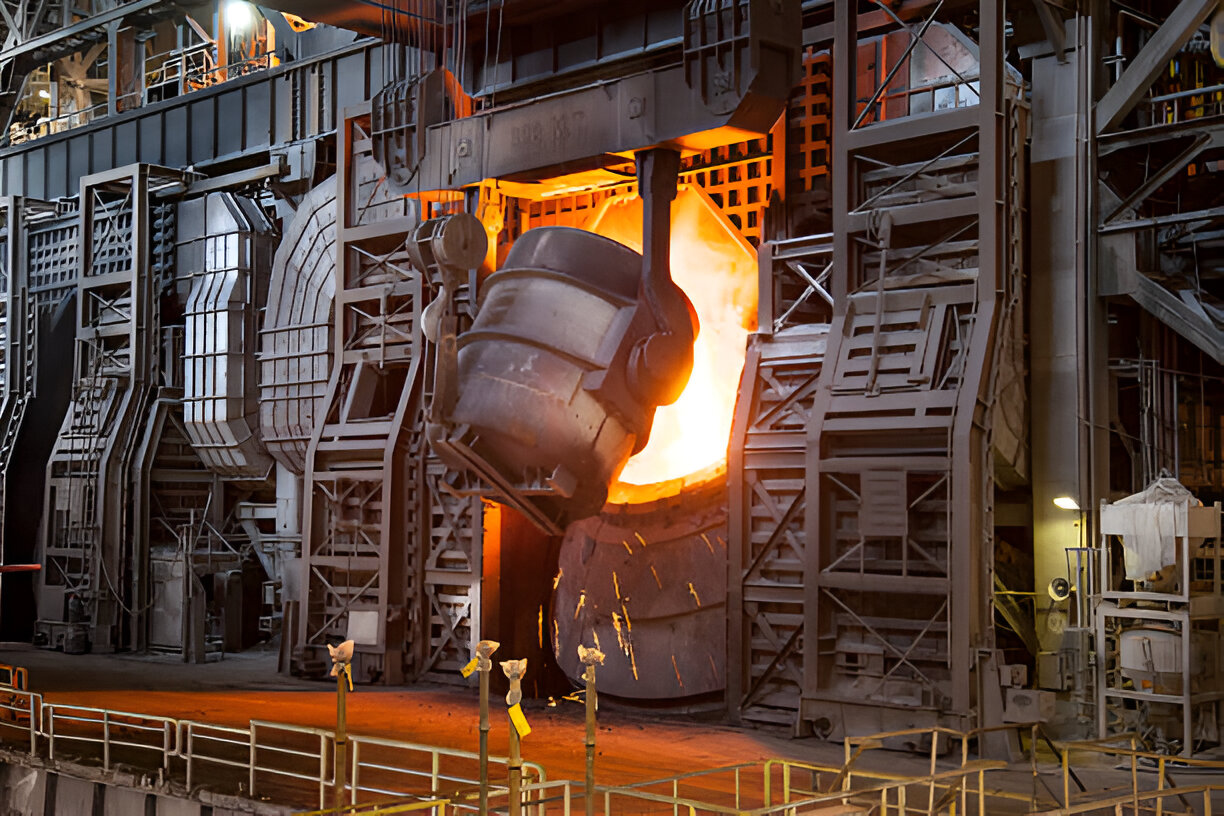
Why Choose Harbor Labs for Forging?
- Global Forging Network
We partner with ISO 9001-certified forging facilities across Asia and Europe, ensuring quality, consistency, and scalability across production runs. - Superior Mechanical Properties
Forged parts exhibit excellent grain alignment, fewer defects, and a higher strength-to-weight ratio — ideal for safety-critical or high-stress environments. - Materials We Forge
Carbon Steel & Alloy Steel
Stainless Steel
Aluminum
Titanium
Brass, Bronze & Copper
High-Performance Alloys (Inconel, Hastelloy) - Engineering Collaboration
From material selection to grain flow simulation, our technical teams provide hands-on support to optimize product geometry and manufacturability. - Efficient, Cost-Effective Production
We balance speed, precision, and cost-efficiency by leveraging digital DFM, tooling support, and supplier integration — reducing cycle time and waste.
Benefits of Forging
Superior mechanical strength and load-bearing capacity
High fatigue and impact resistance
Grain flow alignment for long-term durability
Low porosity and internal defect rates
High repeatability and dimensional precision
Reduced need for machining or post-processing
Excellent material utilization and minimal scrap
Ideal for high-pressure, high-heat, and high-vibration environments
Stronger and lighter parts compared to castings
Suitable for integrating complex geometries in a single operation
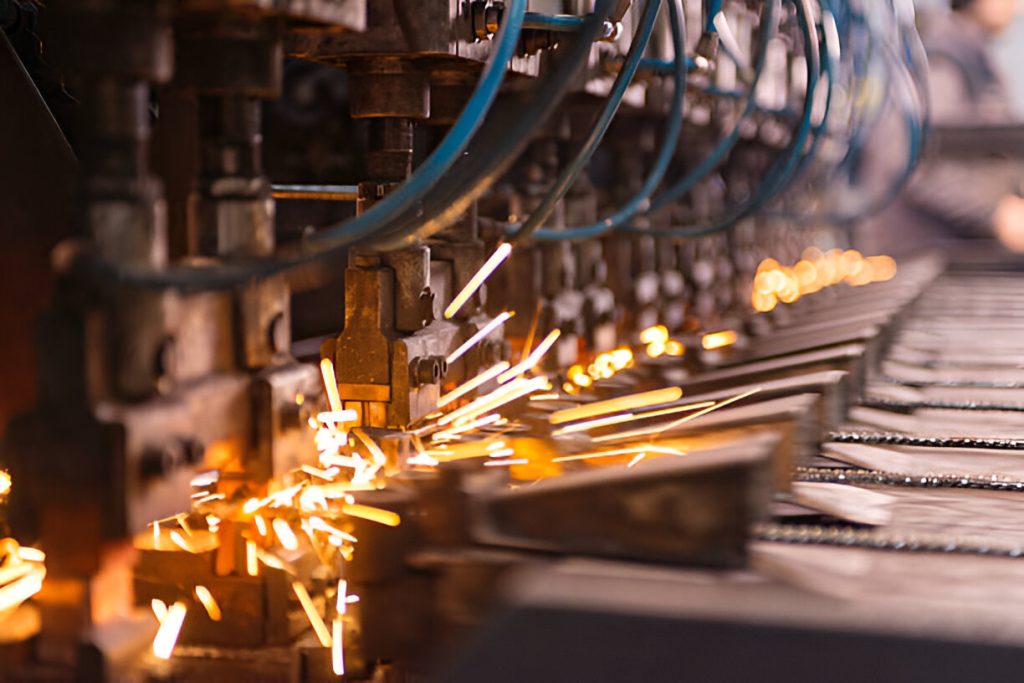
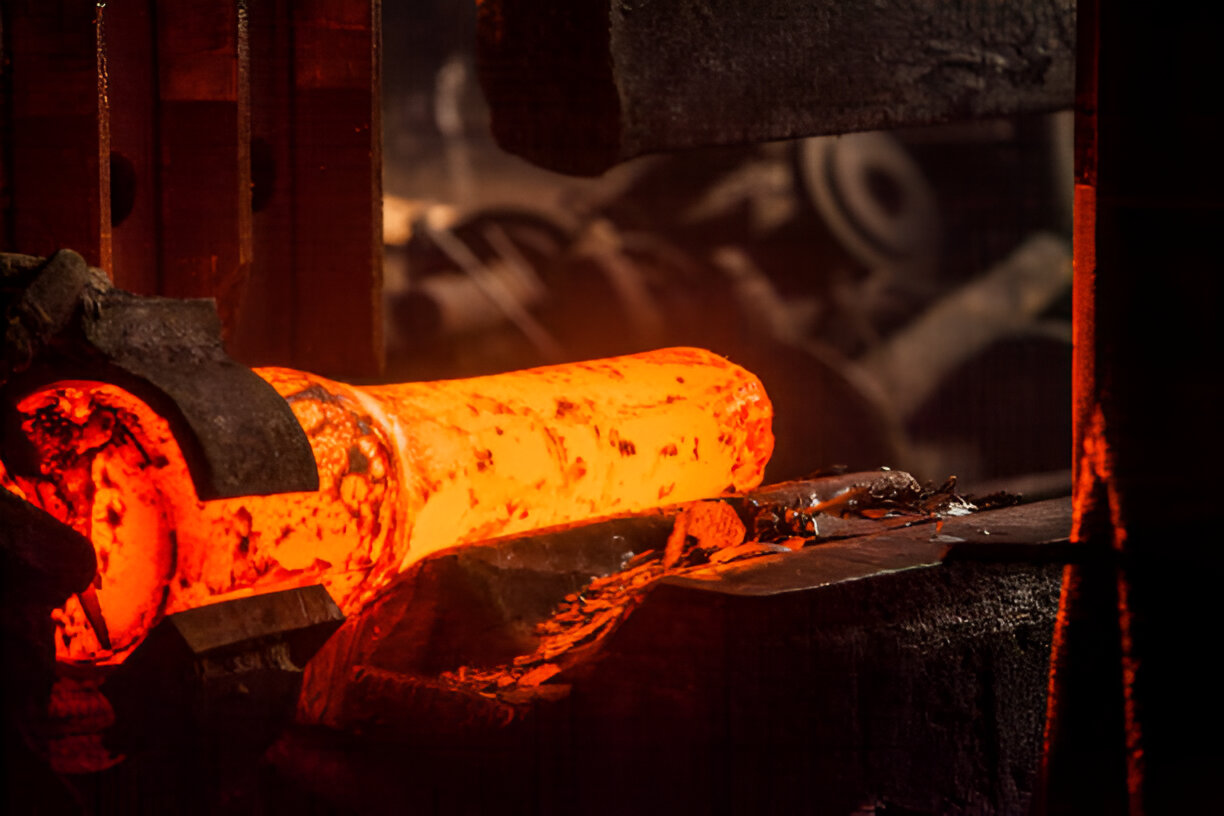
Common Applications
- Automotive: drivetrain components, steering yokes, and control arms
- Construction & Mining: heavy machinery joints and brackets
- Aerospace: turbine discs, landing gear parts
- Oil & Gas: pressure-containing valves and flanges
- Railways: axles, couplers, and linkages
- Agricultural Equipment: blades, tines, and rotating shafts
- Power Transmission: forged gears, bearing races, and hubs