Uncompromising Quality. Engineered for Precision
Global manufacturing success depends not just on price and speed — but on unwavering quality at scale. Harbor Labs provides industry-leading Quality Assurance (QA) and Engineering Support throughout the sourcing and production lifecycle, ensuring every component meets exacting standards. With engineers deployed across all key sourcing regions and QA checkpoints embedded into every process, we minimize defects, maximize consistency, and deliver with confidence — no matter where the product is made. We use a multi-layered quality management approach, built on: Rigorous supplier qualification & requalification Customer-approved tooling designs In-person inspections by sourcing engineers Third-party raw material testing Continuous process monitoring Monthly benchmarking against global standards
The Harbor Labs Quality Difference
- Engineering at Every Step:
Each supplier is supported by a Harbor Labs engineer responsible for tooling integrity, process stability, and part accuracy — resulting in ultra-low PPMI (Parts Per Million Index). - Tooling Accuracy You Can Trust:
We don’t take shortcuts on tooling. Our designs are co-developed with customer input, manufactured to precise tolerances, and verified before mass production begins. - Independent Verification:
We coordinate independent, third-party lab testing of raw materials to ensure compliance with chemical composition, hardness, and structural standards. - Advanced Measurement & Inspection Systems:
From 3D scanning to precision gauges, our suppliers use top-tier inspection equipment supported by our on-ground engineers to validate tolerances and quality.
Global Visibility. Real-Time Updates.
Clients receive 24/7 updates on production quality, shipping timelines, and issue resolution — with proactive communication from our engineering team across continents.
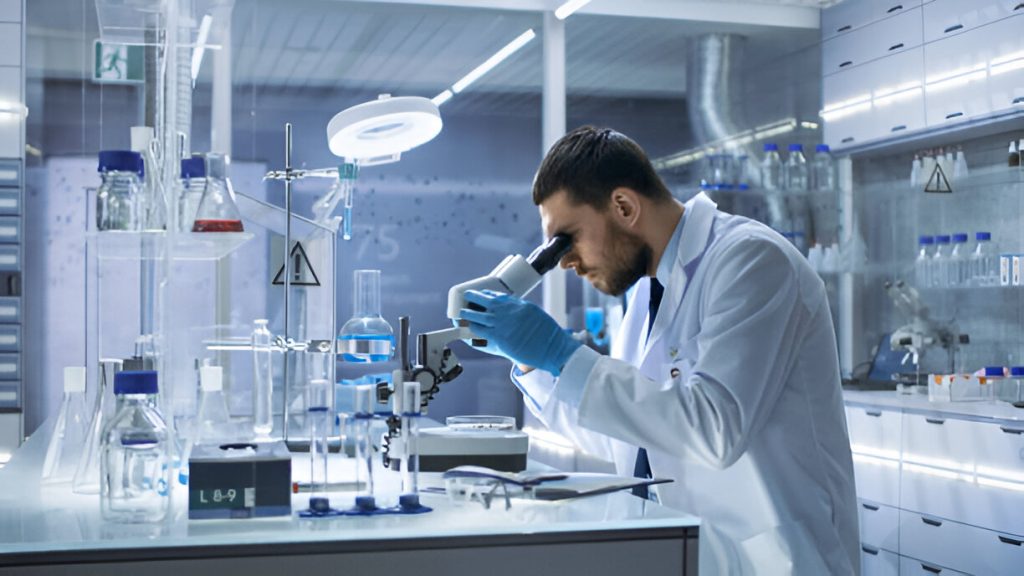
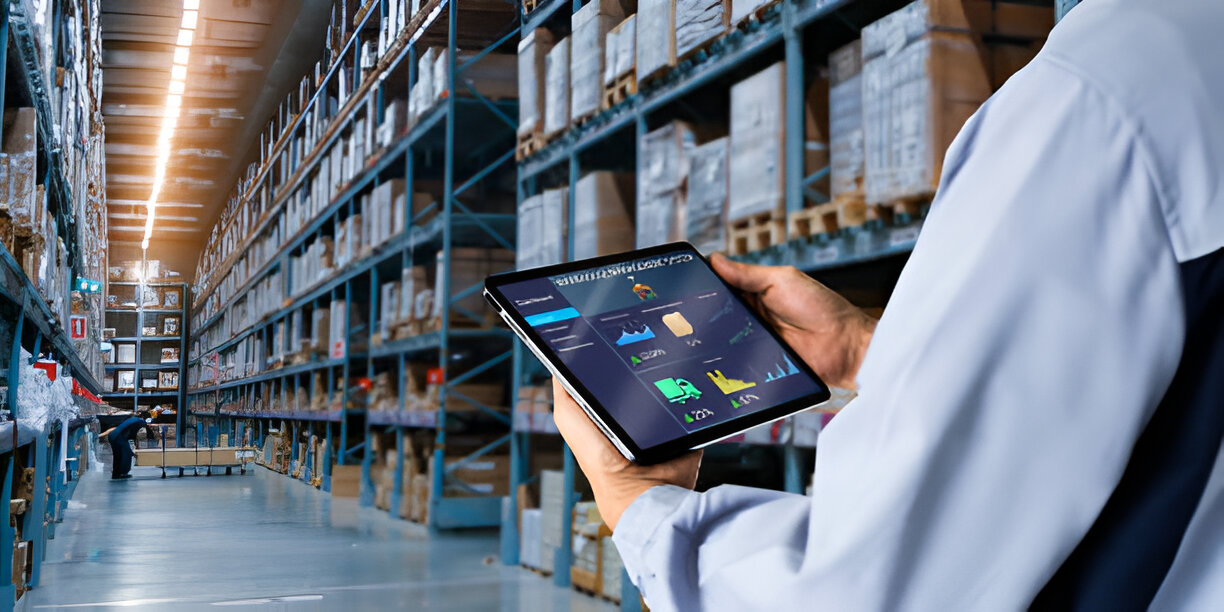
Our Proven Quality Management System Tracks
- Tooling development & change logs
- Critical dimension checks and inspection records
- Material traceability and certificates
- Supplier delivery and defect rates
- Root cause analysis and corrective actions
Client-approved part inspections and sign-offs
CONTINUOUS BENCHMARKING FOR EXCELLENCE
To stay competitive and accountable, Harbor Labs continuously benchmarks its internal processes against industry best practices. We monitor and improve monthly on key KPIs such as:
- On-Time Delivery %
- Defect Rate (PPM)
- Finished Goods Inventory Days
- Warehousing Cost as % of Sales
This ensures we’re not just meeting client expectations — we’re evolving beyond them.